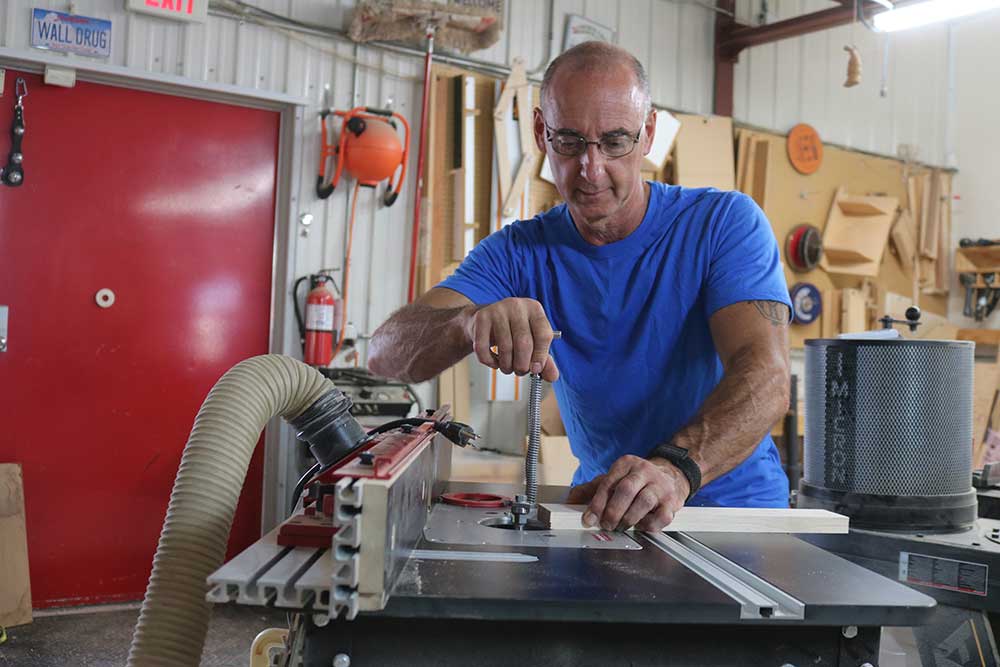
Tom's Knife Making Experience
George VondriskaGeorge’s friend, Tom, dropped in at the shop and spent some time talking about his knife making experiences. Tom isn’t forging blades, he’s adding handles to knife blanks that he buys. This is a great way to make a wonderful custom gift for someone, or to make high quality knives for yourself, without spending a bunch of dough on them.
Where to start
There are many places you can buy knife blanks, and even knife kits that come with everything you need to make your first knife. Tom’s recommendation is that you start with the simplest form of this, which is working with what are called scales. Scales are two small slabs of wood on each side of the knife steel. Prices for knife blanks vary. You can spend under $10, and over $100, depending on what you want.
What you need
Tom’s primary tools for this process are
- Bandsaw
- Drum sander
- Spindle sander
Tom has found that his standard set of woodworking tools serves him well for making the knife handles that he’s worked with so far.
Take this as far as you want
You can spend as much or as little as you want on the knife blank, and use a variety of materials for the handle; wood, plastic, antler, etc. You can also incorporate brass and other materials. Dip your toe in the knife making waters and learn more about how to make knives from wood.
Sources
Here are a few places you can get knife blanks, and other knife making supplies:
Share tips, start a discussion or ask one of our experts or other students a question.
Already a member? Sign in
2 Responses to “Tom's Knife Making Experience”
Explore videos by George Vondriska
You may be interested in
Premium Membership
Unlock exclusive member content from our industry experts.
- 24/7 Access to Premium Woodworking Videos, Projects, and Tips
- Step-by-Step Instructional Demos, Plans, and Tutorials
- 50% Off Video Downloads Purchased in the Woodworkers Guild of America Shop
- 2 Printable Woodworking Plans
Unlock exclusive member content from our industry experts.
- 24/7 Access to Premium Woodworking Videos, Projects, and Tips
- Step-by-Step Instructional Demos, Plans, and Tutorials
- 50% Off Video Downloads Purchased in the Woodworkers Guild of America Shop
- 2 Full-Length Video Downloads to Watch Offline
- 2 Printable Woodworking Plans
Gold Membership
$370 Value
Get everything included in Premium plus exclusive Gold Membership benefits.
- 24/7 Access to Premium Woodworking Videos, Projects, and Tips
- Step-by-Step Instructional Demos, Plans, and Tutorials
- 8 Full-Length Video Downloads to Watch Offline
- 3 Full-Length Woodworking Classes to Keep for Life
- 7 Printable Woodworking Plans
- Discounts on Purchase-to-Own Content in the Woodworkers Guild of America Shop
- Access to Ask the Expert Program
- Exclusive GOLD LIVE Streaming Events
Nice intro for the totally new maker. A couple of tips. A bandsaw is not indispensable. There is a faster and easier way to cut the scales I learned from old timers without the expense of a bandsaw. Place one scale one with temp pins and double stick tape. Then trim it with a straight, 1/4 round or 45 degree router trim bit. Run the bearing on the steel and make a perfect piece just like applying a laminate counter top. Do the other side and then use the pins to finish sand while off the knife. Then epoxy with a perfect fit. Easy and you don't mess up the finish on the knife spine by sanding. Especially nice for store bought blades. Also always finish the front of the scales before epoxy. Its easier to do off the blade so you don't scratch up the blade while sanding the scale. PS: many modern knife makers no longer solder their trick tangs. Takes some practice but most file a press fit bolster. Angle the file to be a larger slot towards the handle and thinner towards the blade. Much nicer and less mess than solder. A little epoxy on the back side keeps any chance of moisture out.
Tom and George, I've been a woodworker/woodturner for decades and now I'm now getting into cast resin and wood stabilization like so many others do either of you two employ those techniques for knife scales?