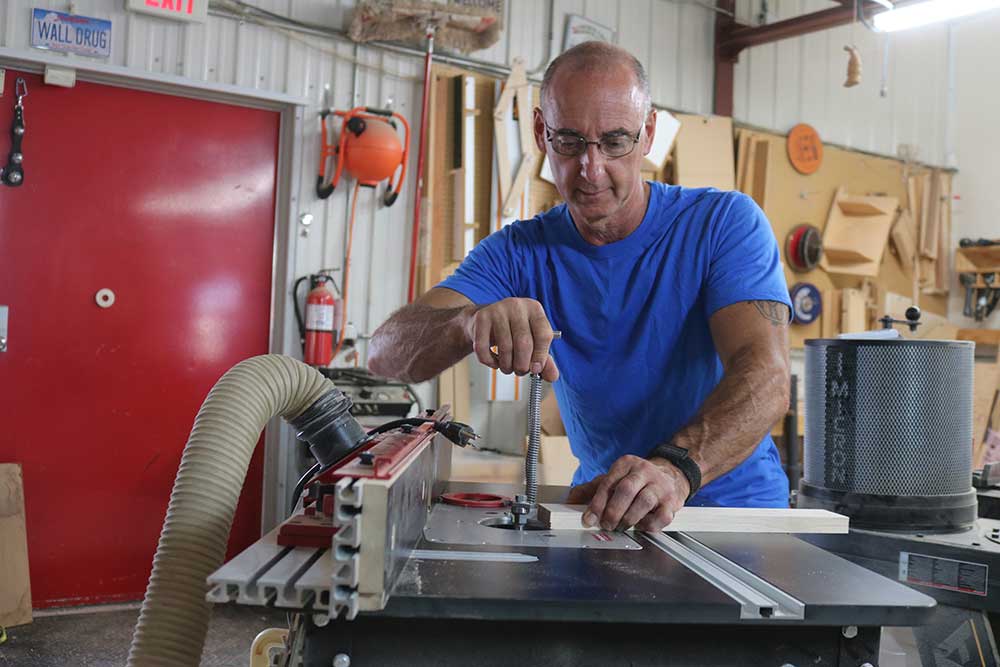
WWGOA LIVE! June 2019
George VondriskaThanks for tuning in. Here’s what we covered.
:40 WWGOA Sweepstakes winners
2:30 Cutting the lid off of a box
9:30 AWFS Las Vegas
9:45 Making long cauls
11:05 Wood for a workbench
12:30 Build a router table with a lift?
13:50 Help with Powermatic jointer
15:30 Pegs on a workbench?
17:15 Trouble with green wood birch bowl
20:10 Plans for George’s workbench
23:30 Matching routers to router tables
25:50 Cutting plexiglass on the tablesaw
28:43 Class on CNC use?
30:12 Trouble with ISOTunes Pro? Their Customer Svc: https://isotunesaudio.com/pages/contact-us
31:10 Biscuits for 90-degree joint
32:50 Euro hinges on inset doors
34:40 Dust collection in George’s shop
37:00 Cutting circles in plexiglass
37:30 Transferring patterns
38:20 Small shop workbench
39:30 Routers and router lifts
41:00 Jointing long boards
42:45 Tightening a table saw blade
43:55 Table saw blade stabilizers?
45:30 Colored woods bleeding into maple
47:40 Staining maple
49:20 Dimensions of George’s cordless tool cabinet
48:45 Does polyurethane get old?
51:20 Filters on dust collectors
52:50 Mitered banding on table top
53:50 Snipe on planers
54:50 Drill chuck fall off drill press
57:08 Plane to buy?
58:10 Making a 1/8” thick glue up
59:20 Drilling a hole with a forstner at 45-degrees
1:01 Micro kerf blades?
1:01:3045-degree joint isn’t flush
1:02 George’s teaching schedule
WWGOA LIVE is brought to you by:
Explore videos by George Vondriska
You may be interested in
Premium Membership
Unlock exclusive member content from our industry experts.
- 24/7 Access to Premium Woodworking Videos, Projects, and Tips
- Step-by-Step Instructional Demos, Plans, and Tutorials
- 50% Off Video Downloads Purchased in the Woodworkers Guild of America Shop
- 2 Printable Woodworking Plans
Unlock exclusive member content from our industry experts.
- 24/7 Access to Premium Woodworking Videos, Projects, and Tips
- Step-by-Step Instructional Demos, Plans, and Tutorials
- 50% Off Video Downloads Purchased in the Woodworkers Guild of America Shop
- 2 Full-Length Video Downloads to Watch Offline
- 2 Printable Woodworking Plans
Gold Membership
$370 Value
Get everything included in Premium plus exclusive Gold Membership benefits.
- 24/7 Access to Premium Woodworking Videos, Projects, and Tips
- Step-by-Step Instructional Demos, Plans, and Tutorials
- 8 Full-Length Video Downloads to Watch Offline
- 3 Full-Length Woodworking Classes to Keep for Life
- 7 Printable Woodworking Plans
- Discounts on Purchase-to-Own Content in the Woodworkers Guild of America Shop
- Access to Ask the Expert Program
- Exclusive GOLD LIVE Streaming Events
Share tips, start a discussion or ask one of our experts or other students a question.
Already a member? Sign in
No Responses to “WWGOA LIVE! June 2019”