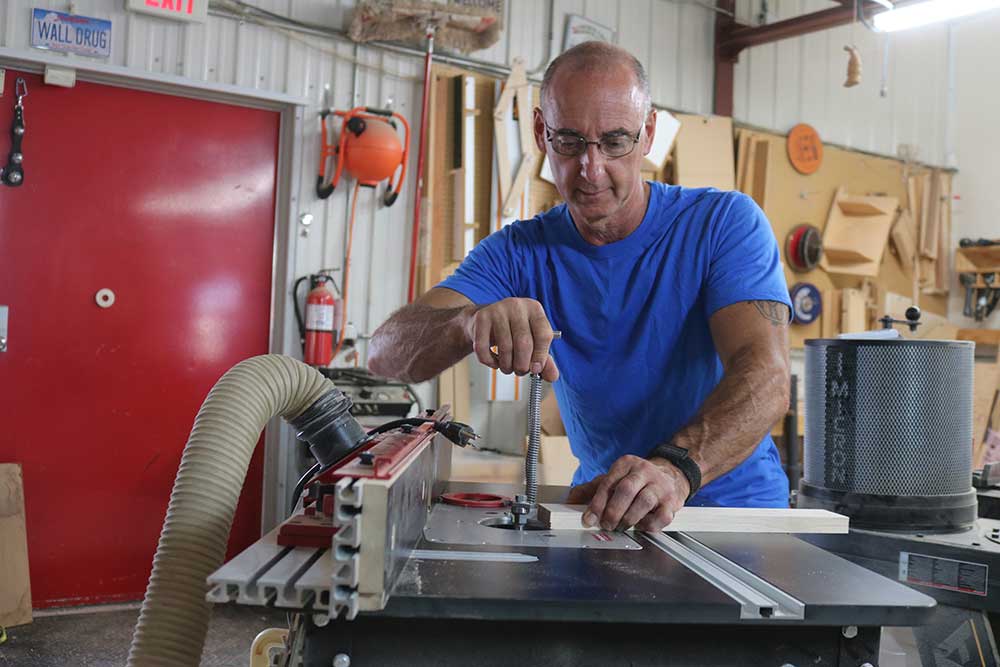
WWGOA Fall 2023 Product Showcase
George VondriskaJoin George Vondriska for the WWGOA Fall 2023 Product Showcase! Tune in for demonstrations to stay up-to-date on the newest and most innovative woodworking products from Penn State Industries, Arbor Tech, ISOtunes, BORA, Woodmaster Tool, Mullet Tools, and Fuji Spray.
Don’t forget to sign up for the free WWGOA newsletter to be notified via email about future LIVE events.
WWGOA Product Showcase Sponsors
Penn State Industries
Arbor Tech
ISOtunes
BORA/Affinity Tool
Woodmaster Tool
Mullet Tools
Fuji Spray
Explore videos by George Vondriska
 
 
 
 
 
 
 
 
 
 
 
 
 
 
 
 
 
 
 
 
 
 
 
 
You may be interested in
 
 
 
 
 
 
 
 
 
 
 
 
 
 
 
 
 
 
 
 
 
 
 
 
 
Premium Membership
Unlock exclusive member content from our industry experts.
- 24/7 Access to Premium Woodworking Videos, Projects, and Tips
- Step-by-Step Instructional Demos, Plans, and Tutorials
- 50% Off Video Downloads Purchased in the Woodworkers Guild of America Shop
- 2 Printable Woodworking Plans
Unlock exclusive member content from our industry experts.
- 24/7 Access to Premium Woodworking Videos, Projects, and Tips
- Step-by-Step Instructional Demos, Plans, and Tutorials
- 50% Off Video Downloads Purchased in the Woodworkers Guild of America Shop
- 2 Full-Length Video Downloads to Watch Offline
- 2 Printable Woodworking Plans
Gold Membership
$370 Value
Get everything included in Premium plus exclusive Gold Membership benefits.
- 24/7 Access to Premium Woodworking Videos, Projects, and Tips
- Step-by-Step Instructional Demos, Plans, and Tutorials
- 8 Full-Length Video Downloads to Watch Offline
- 3 Full-Length Woodworking Classes to Keep for Life
- 7 Printable Woodworking Plans
- Discounts on Purchase-to-Own Content in the Woodworkers Guild of America Shop
- Access to Ask the Expert Program
- Exclusive GOLD LIVE Streaming Events
Get exclusive premium content! Sign up for a membership now!
Share tips, start a discussion or ask one of our experts or other students a question.
Already a member? Sign in
No Responses to “WWGOA Fall 2023 Product Showcase”