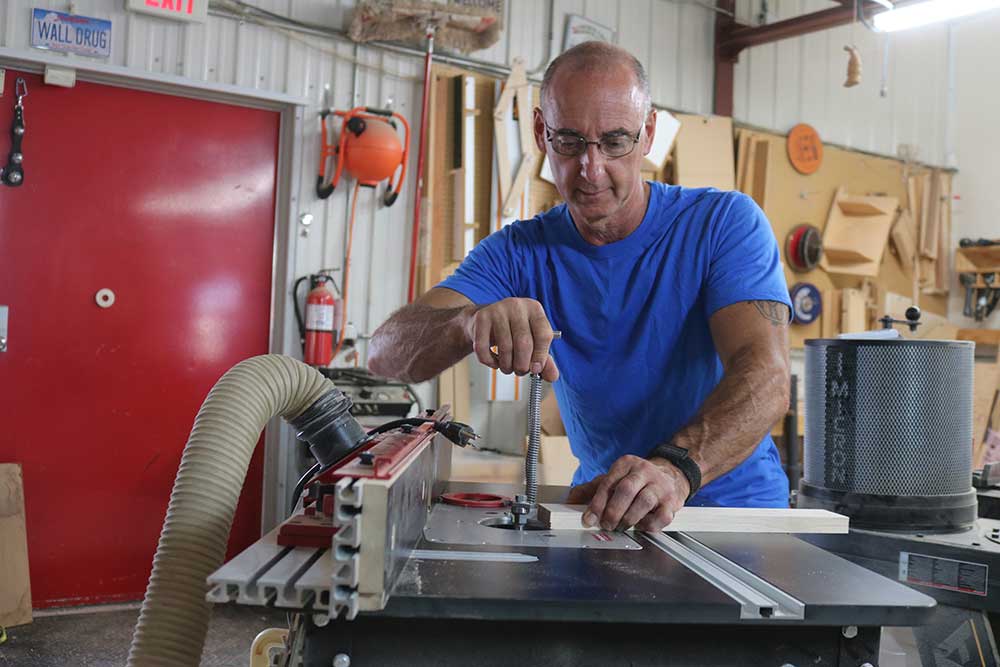
V-Carving Artwork & Letters with a CNC Router
George VondriskaV-carving on a CNC wood router creates an amazing hand carved look. The letters or artwork you V-carve will stand in relief of the background. This may look complicated, but it’s pretty straight forward, with a little instruction. We’re here to provide the instruction. We’ll show you how to create the design on VCarve software, and how to set up the cuts on a Laguna CNC machine.
Importing artwork
Amazingly, you can grab virtually any clip art from the web and import it into VCarve to work with. The clip art will need to be changed to vectors so it can be CNC cut, and we’ll show you how to do that, and how to refine the design so it looks good after it’s been cut.
Lettering
VCarve software includes a wide variety of fonts. Once the font has been chosen, you’ll learn how to locate the lettering on the project, and change its size as needed.
V-Carve on the CNC wood router
Setting up the design to create the v-carve includes correctly selecting the artwork and lettering, and choosing the right router bits. You’ll learn how to use a clearance tool to remove most of the waste, and what type of cutter makes the v-carve pop.
Set up the CNC machine
Next you’ll learn to correctly install router bits on the CNC machine, and how to zero the X, Y, and Z axes. You’ll also learn to how to secure your work to the table.
Want to know more?
If you’re wondering if a CNC is a worthwhile investment for your shop, check out our video that provides an overview of what a CNC machine can do for you. If you’re looking for help using VCarve software, check out our video about CNC machine programming tips.
Share tips, start a discussion or ask one of our experts or other students a question.
Already a member? Sign in
2 Responses to “V-Carving Artwork & Letters with a CNC Router”
Explore videos by George Vondriska
You may be interested in
Premium Membership
Unlock exclusive member content from our industry experts.
- 24/7 Access to Premium Woodworking Videos, Projects, and Tips
- Step-by-Step Instructional Demos, Plans, and Tutorials
- 50% Off Video Downloads Purchased in the Woodworkers Guild of America Shop
- 2 Printable Woodworking Plans
Unlock exclusive member content from our industry experts.
- 24/7 Access to Premium Woodworking Videos, Projects, and Tips
- Step-by-Step Instructional Demos, Plans, and Tutorials
- 50% Off Video Downloads Purchased in the Woodworkers Guild of America Shop
- 2 Full-Length Video Downloads to Watch Offline
- 2 Printable Woodworking Plans
Gold Membership
$370 Value
Get everything included in Premium plus exclusive Gold Membership benefits.
- 24/7 Access to Premium Woodworking Videos, Projects, and Tips
- Step-by-Step Instructional Demos, Plans, and Tutorials
- 8 Full-Length Video Downloads to Watch Offline
- 3 Full-Length Woodworking Classes to Keep for Life
- 7 Printable Woodworking Plans
- Discounts on Purchase-to-Own Content in the Woodworkers Guild of America Shop
- Access to Ask the Expert Program
- Exclusive GOLD LIVE Streaming Events
In the video it didn't appear that you had a sacrificial board between the work piece and the bed of the CNC. Don't you need that when making cuts all the way through the work piece to prevent the bed from getting chewed up?
these cnc videos stop at about 19 or 20 minutes in and will not start up again