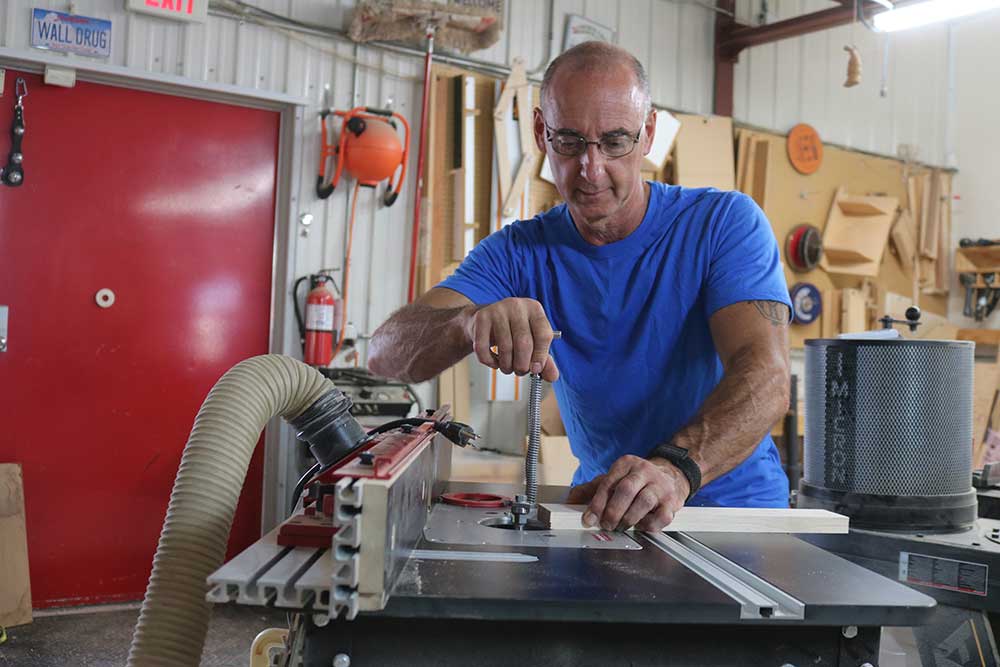
Jointing Opposite Faces
George VondriskaI get asked, all the time, about using a jointer to face joint opposing faces of a rough sawn lumber. Will this work? Can it be done? If not, why not? The answer; a jointer will do a great job of getting two opposing faces smooth and straight, but it WON’T guarantee that the two faces are parallel to each other. The problem is that, if the two faces aren’t parallel to start with (and from a sawmill, they won’t be) you can’t make them parallel on a jointer. This is a bad start to a woodworking project.
The right approach
This is a great application for a jointer and planer working together. Once you have one face of the board flat, take it to the planer and you’ll be guaranteed flat faces, parallel faces, and uniform thickness.
When SHOULD I use a jointer?
Although the jointer isn’t the right tool for face jointing opposing faces of rough sawn lumber, it’s great for lots of other jobs, and a must-have tool for getting your lumber true. We’ve got lots of great info if you’re wondering “what is a jointer used for?”
Jointer techniques
Jointers aren’t the toughest tools to master, but there are subtleties that will help your work come out better. Be sure you’re confident about how to use a jointer before diving in on your first project.
For more info
Learn more about how to machine your rough sawn lumber perfectly square by watching Post Haste Project: How to Square a Board.
Share tips, start a discussion or ask one of our experts or other students a question.
Already a member? Sign in
3 Responses to “Jointing Opposite Faces”
Explore videos by George Vondriska
You may be interested in
Premium Membership
Unlock exclusive member content from our industry experts.
- 24/7 Access to Premium Woodworking Videos, Projects, and Tips
- Step-by-Step Instructional Demos, Plans, and Tutorials
- 50% Off Video Downloads Purchased in the Woodworkers Guild of America Shop
- 2 Printable Woodworking Plans
Unlock exclusive member content from our industry experts.
- 24/7 Access to Premium Woodworking Videos, Projects, and Tips
- Step-by-Step Instructional Demos, Plans, and Tutorials
- 50% Off Video Downloads Purchased in the Woodworkers Guild of America Shop
- 2 Full-Length Video Downloads to Watch Offline
- 2 Printable Woodworking Plans
Gold Membership
$370 Value
Get everything included in Premium plus exclusive Gold Membership benefits.
- 24/7 Access to Premium Woodworking Videos, Projects, and Tips
- Step-by-Step Instructional Demos, Plans, and Tutorials
- 8 Full-Length Video Downloads to Watch Offline
- 3 Full-Length Woodworking Classes to Keep for Life
- 7 Printable Woodworking Plans
- Discounts on Purchase-to-Own Content in the Woodworkers Guild of America Shop
- Access to Ask the Expert Program
- Exclusive GOLD LIVE Streaming Events
What about just using a planer on both sides of 14' rough cut lumber then rip one side straight, flip and rip the other side, 14' lumber is kinda big to run over a jointer you can do this on over sized parts then trim the waste off to size. This should give 4 sides squar or will it be out? At what point is wood good enough. Because it moves, metal also moves just not as much. I worked in a machine shop for 7 Years trust me metal moves. Heat and cold will change metal just not as far as wood will. I also use a digital caliper in woodworking but seriously 5thou tolrances in wood is ridiculous. It might work for jigs to set them up but don't count on it staying that way. Aircraft alumian 6061 and plexi glass or HDPE plastic. Most carbide cutting tools will work on this type of materials I'd use a 80 tooth no hook blade ment for this type of material.
I seek to always get wedge shaped boards when face jointing. The jointer removes more material from the infeed end of the board no matter how much pressure, or where the pressure is applied on the board as it is fed over the cutter.
Can you use a thickness planer to accomplish both tasks? I make signs on a CNC. I purchase 2x12 redwood boards. They are air dried, but I let them sit for while and dry out further. Often they are cupped to some degree. I just run them through the thickness planer, alternating sides until pencil lines I've placed upon both sides widths, are gone. It seems to work.