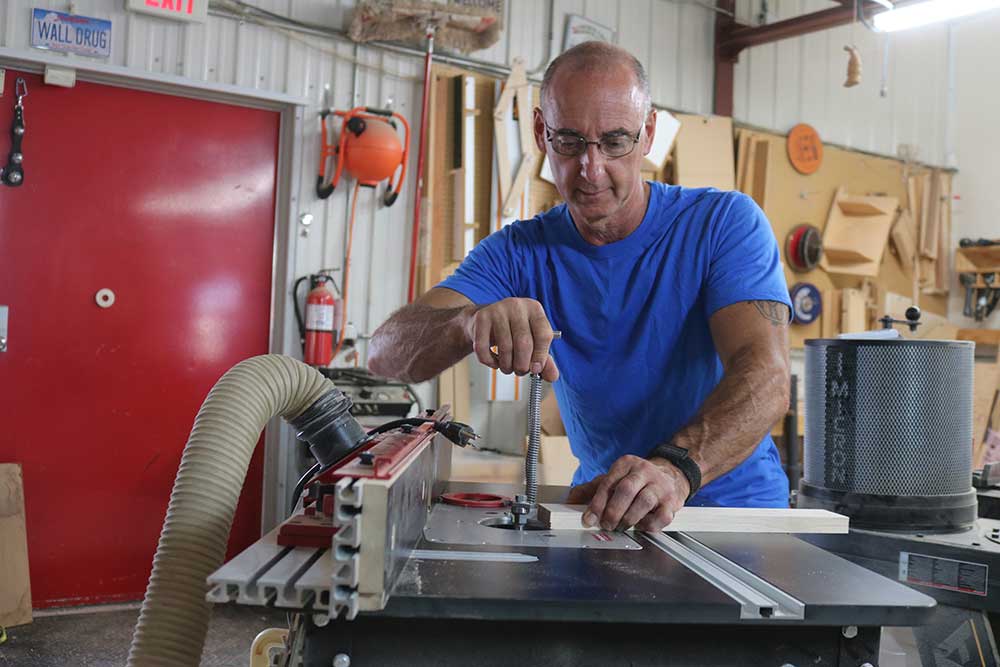
WWGOA LIVE! April 2018
George VondriskaTonight may have seen a record number of questions answered! Thanks for watching, and submitting such great woodworking questions.
:45 Sharpen and use a scraper
8:20 What to do with sawdust
11:00 Setting jointer knives
14:57 Turning birds eye maple
15:35 CNC machine recommendation
17:39 Chip carving
18:40 Finish for poplar outdoor furniture
19:20 Home center plywood
21:32 Getting good cuts from a jig saw; Down cutting jig saw blades
28:55 Best glue for bent laminations
30:50 Spraying paint; airless or HVLP Floetrol
32:31 Filling dimples in cherry; Timbermate cherry filler
34:00 Working with green treated lumber
35:16 Hand held router info
36:40 George rough looking hands 😊
36:55 How do you know planer knives are dull?
38:34 Levelling end grain cutting boards; Infinity Dado and Planer bit
Check this video: Flattening Large Wood Slabs with a Router
42:40 Fence position on a vertical panel raiser
44:00 Jointer or planer?
45:20 HVLP compressor or turbine?
47:20 Help on building tables
48:09 Good countersinks
48:57 RPM for router bits
50:36 Logs to lumber on a bandsaw. Check this video: Cutting a Log on a Bandsaw
54:37 Selling tools
55:00 Levelling slabs
57:00 Preventing rust on tools
58:04 Banding solid wood four sides
59:50 Turned plugs out of round
1:01 Joinery for cabinets
1:02:13 Face jointing material wider than your jointer
Explore videos by George Vondriska
Premium Membership
Unlock exclusive member content from our industry experts.
- 24/7 Access to Premium Woodworking Videos, Projects, and Tips
- Step-by-Step Instructional Demos, Plans, and Tutorials
- 50% Off Video Downloads Purchased in the Woodworkers Guild of America Shop
- 2 Printable Woodworking Plans
Unlock exclusive member content from our industry experts.
- 24/7 Access to Premium Woodworking Videos, Projects, and Tips
- Step-by-Step Instructional Demos, Plans, and Tutorials
- 50% Off Video Downloads Purchased in the Woodworkers Guild of America Shop
- 2 Full-Length Video Downloads to Watch Offline
- 2 Printable Woodworking Plans
Gold Membership
$370 Value
Get everything included in Premium plus exclusive Gold Membership benefits.
- 24/7 Access to Premium Woodworking Videos, Projects, and Tips
- Step-by-Step Instructional Demos, Plans, and Tutorials
- 8 Full-Length Video Downloads to Watch Offline
- 3 Full-Length Woodworking Classes to Keep for Life
- 7 Printable Woodworking Plans
- Discounts on Purchase-to-Own Content in the Woodworkers Guild of America Shop
- Access to Ask the Expert Program
- Exclusive GOLD LIVE Streaming Events
Share tips, start a discussion or ask one of our experts or other students a question.
Already a member? Sign in
No Responses to “WWGOA LIVE! April 2018”