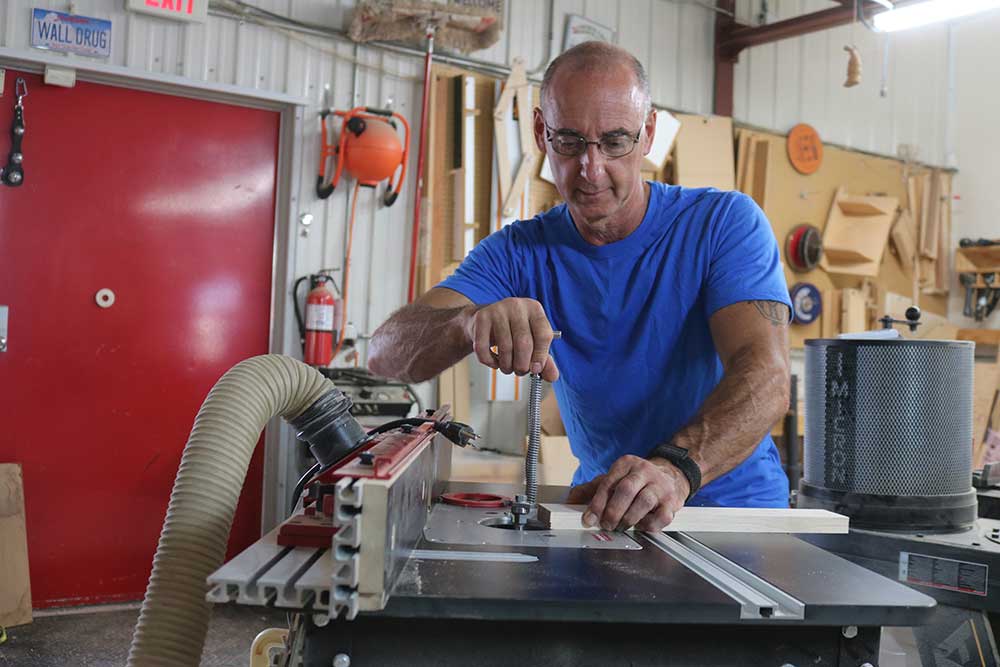
WWGOA LIVE! July 2018
George VondriskaA stormy night, which made for a great evening to be in the shop answering your questions. Thanks for watching!
00:40 Alternate growth rings on a glue up?
2:44 Material for dressers?
3:20 Face jointing
7:30 Odor from finish
9:00 Is elm a good wood?
9:35 George’s favorite hearing protection
11:00 Squaring up a frame
11:30 Spaceballs
12:50 Drywalls screws vs wood screws
15:15 Steel wool for abrading between finish coats?
17:15 Uses for OSB
18:24 Start with a table saw or miter saw
19:00 George’s new workbench
22:00 Inexpensive dust collection
23:50 Hand pressure when jointing
25:10 How deep for mortises and dowel holes?
25:50 Gluing over an area that already has glue on it
26:30 Staining blue
30:08 Maintaining a rustic look
30:48 Precision for puzzles
32:00 Dust pipe size
33:12 Grit for sanding between coats
33:44 A closer look at George’s bench
36:40 Pallet wood
37:14 Bowl finishes
39:26 More uses for OSB
40:00 George’s teaching history
40:40 Apple wood
41:30 Bowl blanks with no bandsaw
42:50 Ply laminate splits
43:20 Knocking down gloss
43:40 Best drawer construction method
44:30 George’s transition plane
45:45 Uniform stain color
47:00 Jointer procedure
42:12 Canoe
48:50 Cleaning up aniline dye
51:20 Sawdust to fire blocks
53:00 George’s canoe project
56:30 Electric chainsaw
59:30 Adding legs to large slabs
01:00:00 Japanese pull saws
Explore videos by George Vondriska
You may be interested in
Premium Membership
Unlock exclusive member content from our industry experts.
- 24/7 Access to Premium Woodworking Videos, Projects, and Tips
- Step-by-Step Instructional Demos, Plans, and Tutorials
- 50% Off Video Downloads Purchased in the Woodworkers Guild of America Shop
- 2 Printable Woodworking Plans
Unlock exclusive member content from our industry experts.
- 24/7 Access to Premium Woodworking Videos, Projects, and Tips
- Step-by-Step Instructional Demos, Plans, and Tutorials
- 50% Off Video Downloads Purchased in the Woodworkers Guild of America Shop
- 2 Full-Length Video Downloads to Watch Offline
- 2 Printable Woodworking Plans
Gold Membership
$370 Value
Get everything included in Premium plus exclusive Gold Membership benefits.
- 24/7 Access to Premium Woodworking Videos, Projects, and Tips
- Step-by-Step Instructional Demos, Plans, and Tutorials
- 8 Full-Length Video Downloads to Watch Offline
- 3 Full-Length Woodworking Classes to Keep for Life
- 7 Printable Woodworking Plans
- Discounts on Purchase-to-Own Content in the Woodworkers Guild of America Shop
- Access to Ask the Expert Program
- Exclusive GOLD LIVE Streaming Events
Share tips, start a discussion or ask one of our experts or other students a question.
Already a member? Sign in
No Responses to “WWGOA LIVE! July 2018”