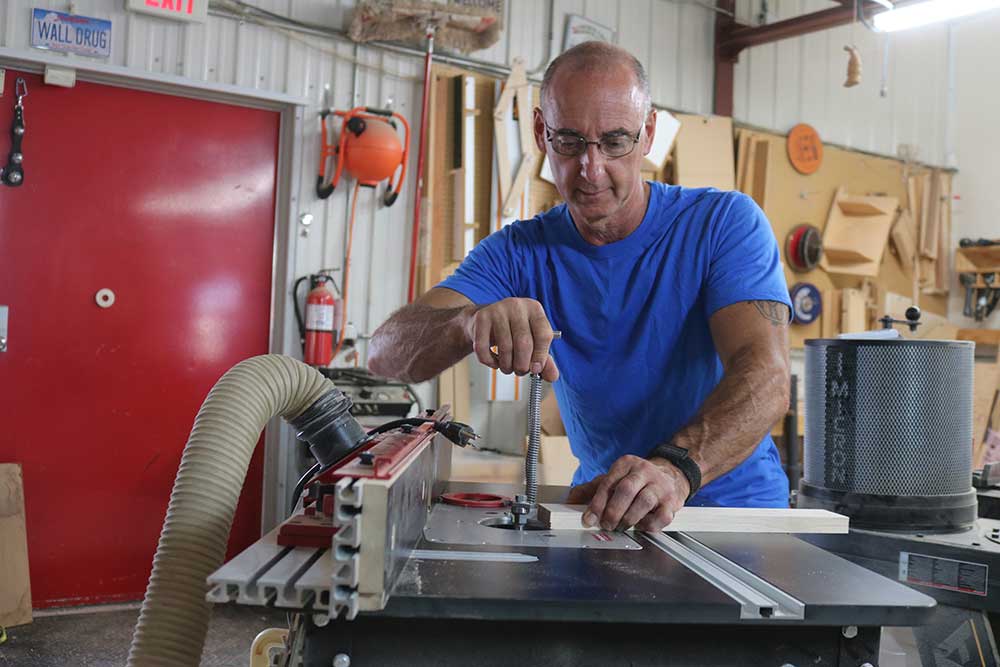
WWGOA LIVE! May 2018
George VondriskaWinter in Wisconsin has (finally) ended. A beautiful evening, and great night in the shop answering questions and running tools.
Here’s what we did:
1:57 Wood identification
3:47 Mix dewaxed shellac?
5:40 Jointer use for flat glue ups
11:53 Finishing products in Columbia
12:30 Rabbeting a dowel
17:34 Finish on a mesquite coffee table
19:14 Core quality on plywood
21:43 George’s tattoo
24:06 DeWalt and Wen planer
26:40 Router lift education
31:45 Jointer or planer for parallel faces?
33:11 Spraying primer and top coats
33:43 Sears router table review?
34:15 Good beginner projects
35:46 Finish for a log candle holder
36:45 Upgrade to helical cutter heads?
38:04 Door thickness? Material for paint grade doors
39:22 Preventing chipping when cutting veneered material
47:20 Uses for butternut
48:13 SketchUp
49:13 Parallelogram vs dovetail way jointers
52:40 Storage on cabinet doors
55:30 Plans for shop storage units
57:57 Tablesaw choice
58:30 Snipe on planers
1:01 Scheduling of live events
Explore videos by George Vondriska
Premium Membership
Unlock exclusive member content from our industry experts.
- 24/7 Access to Premium Woodworking Videos, Projects, and Tips
- Step-by-Step Instructional Demos, Plans, and Tutorials
- 50% Off Video Downloads Purchased in the Woodworkers Guild of America Shop
- 2 Printable Woodworking Plans
Unlock exclusive member content from our industry experts.
- 24/7 Access to Premium Woodworking Videos, Projects, and Tips
- Step-by-Step Instructional Demos, Plans, and Tutorials
- 50% Off Video Downloads Purchased in the Woodworkers Guild of America Shop
- 2 Full-Length Video Downloads to Watch Offline
- 2 Printable Woodworking Plans
Gold Membership
$370 Value
Get everything included in Premium plus exclusive Gold Membership benefits.
- 24/7 Access to Premium Woodworking Videos, Projects, and Tips
- Step-by-Step Instructional Demos, Plans, and Tutorials
- 8 Full-Length Video Downloads to Watch Offline
- 3 Full-Length Woodworking Classes to Keep for Life
- 7 Printable Woodworking Plans
- Discounts on Purchase-to-Own Content in the Woodworkers Guild of America Shop
- Access to Ask the Expert Program
- Exclusive GOLD LIVE Streaming Events
Share tips, start a discussion or ask one of our experts or other students a question.
Already a member? Sign in
No Responses to “WWGOA LIVE! May 2018”