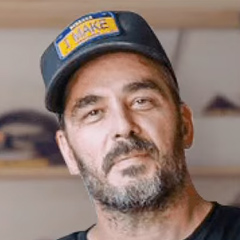
Making a Knife from a Saw Blade
Jimmy DiRestaCarbide-tipped table saw blades get to a point where they can no longer be sharpened. Then what? If you’ve got old saw blades laying around your shop, here’s a project for you. Make a table saw blade knife!
Steel quality
The durability of a carbide-tipped saw blade comes from the carbide, not the steel plate. So, the plate isn’t the BEST knife-making material in the world, but it isn’t bad. A file test will tell you a lot about the quality of the metal, and heating and quenching after the knife is made will help a lot. Blades that are not carbide-tipped are most likely made from a higher quality steel.
Cutting and shaping the blade
You can do all the cutting with an angle grinder and cut off wheel. Make shallow and gentle cuts so you don’t snap the cut off wheel. Finalize the shape and polish the knife using flap sander discs on your angle grinder.
Get a handle on it
Use a good hardwood for the handle. If you want to add pins like we did, brazing rod works great. Adhere the handle to the blank with two-part epoxy, let it cure, then shape and seal the handle.
More than knives
This is a fun process and can be used for more than table saw blade knives. You can make other shop-made tools, like a custom shaped scraper. It’d also be fun to get a kid involved and help them make their first knife.
More on knife making
Knife making can go in a lot of directions. My friend, Tom, has been making knives for a long time and is happy to talk about it. I’ve been buying knife blanks for years and making my own handles, including all of my kitchen knives.
Unlock Your Woodworking Potential!
Sign up for our newsletter for endless woodworking inspiration! Become a member today and gain access to a world of craftsmanship.
Share tips, start a discussion or ask one of our experts or other students a question.
Already a member? Sign in
3 Responses to “Making a Knife from a Saw Blade”
Explore videos by Jimmy DiResta
You may be interested in
Premium Membership
Unlock exclusive member content from our industry experts.
- 24/7 Access to Premium Woodworking Videos, Projects, and Tips
- Step-by-Step Instructional Demos, Plans, and Tutorials
- 50% Off Video Downloads Purchased in the Woodworkers Guild of America Shop
- 2 Printable Woodworking Plans
Unlock exclusive member content from our industry experts.
- 24/7 Access to Premium Woodworking Videos, Projects, and Tips
- Step-by-Step Instructional Demos, Plans, and Tutorials
- 50% Off Video Downloads Purchased in the Woodworkers Guild of America Shop
- 2 Full-Length Video Downloads to Watch Offline
- 2 Printable Woodworking Plans
Gold Membership
$370 Value
Get everything included in Premium plus exclusive Gold Membership benefits.
- 24/7 Access to Premium Woodworking Videos, Projects, and Tips
- Step-by-Step Instructional Demos, Plans, and Tutorials
- 8 Full-Length Video Downloads to Watch Offline
- 3 Full-Length Woodworking Classes to Keep for Life
- 7 Printable Woodworking Plans
- Discounts on Purchase-to-Own Content in the Woodworkers Guild of America Shop
- Access to Ask the Expert Program
- Exclusive GOLD LIVE Streaming Events
This is a great shop guy or shop girl project. 😊
A nice overview on making blades from a sawblade. I have made several Plane (hand plane) irons from old saw blades before. The one thing that surprised me with this video was that they didn't finish the heat treating of the blades. After the quench the blades should have been put into an oven. The temp brought up to 400 degrees F and held there for an hour. Then allow to cool to room temperature. This secondary process keeps the blades from being brittle and lessens the chances of the cracking or chipping if dropped.
A very good overview of making your own knife from a saw blade. In 1981 I made a chef's knife from a big "buzz saw" blade and it is still in use today. While at Stout in the late 70's the Metals Instructor, Hank Thomas had a class that included knife making and we were able to use all of the furnaces and equipment that the metallurgy classes used so we could really control the quality of our knives. Great video! Cal Fischer 1980 Stout grad.