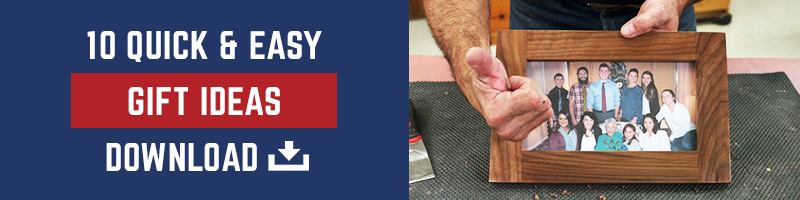
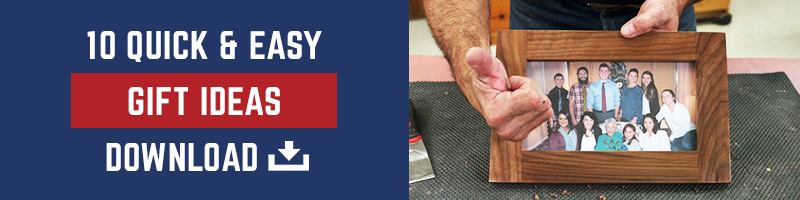
Already a member? Sign in
Unlock exclusive member content from our industry experts.
Unlock exclusive member content from our industry experts.
Get everything included in Premium plus exclusive Gold Membership benefits.
Enter your sign in info below
Excellent info! I try to judge what my time is worth and go from there. Materials can be very expensive, depending on what you use for parts. I also assure the customer that I want them to be very happy with the work I do, too…I will not be the cheapest guy, but I also won’t be the most expensive. I take my time and I do the job right! A good name in the carpentry business goes a LONG way in securing future jobs as well!
Everyone tells me my prices are too low. Thanks for the help.
Pricing. Sale items
Hobby now....extra cash later on to supplement SS.
I have been a member for about 5 years now, and I find that I usually underestimate how much wood I need for a project, even though I add 20-25% overage from my board foot calculations. Why do I always seem to short myself and have to go buy more wood?
I had a friend that works for a <a href="https://www.nhance.com/greenvillewood/cabinet-door-replacement-in-woodruff-sc/" rel="nofollow ugc">cabinet door replacement</a> company. Even though he didn't actually make and sell any products, he explained that carpenters are few and far between and the hourly rate just kept going up for him and his skillset. Thinking to switch over from my fab job to try this! Thanks for the article.
For years I've been undercharging for my services, I have been pricing based on this, cost of materials double it and then add 50% roughly 25% cheaper, I'm guessing the exact same methodology is the norm throughout the world and will be working on that basis from now on
How to price woodwork items
I a few weeks ago sent a comment on pricing custom projects where one's skill level is hard to match in the market and got a response that the comment was awaiting moderation, but since then I have seen no response.
Dear George, Your article on pricing of woodwork was quite interesting and educative in so far as it related to, in my perception, general woodworking. My question comes in the form of, how do I price my work if it is custom, and my skill level is very high as to make the pieces that I make rare?