New
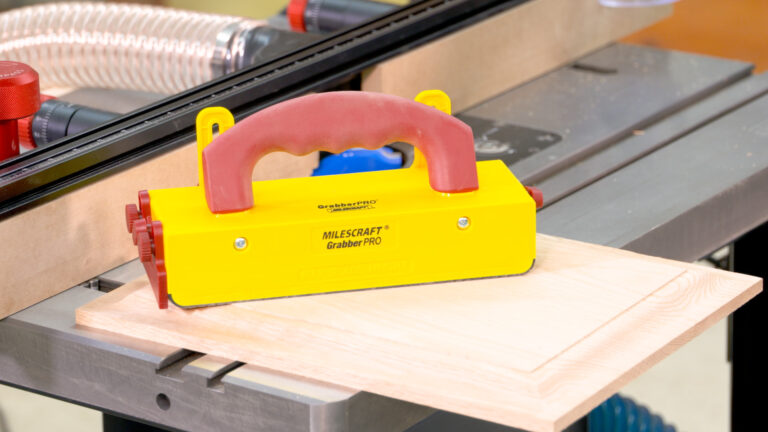
watch
Making Blind Cuts Safely
Video
6 mins